Quality Assurance
Management
Social Issue
In recent years, there has been growing public concern over product quality and safety. Casio remains keenly aware that it must do its very best for customers. Casio believes it can offer trust and peace of mind to customers by providing high-quality, exceptionally safe products.
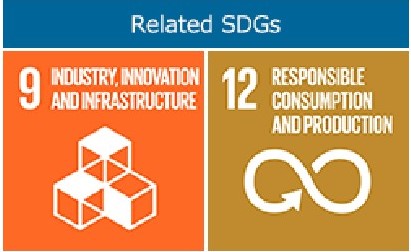
Importance for the Casio Group
Once an accident related to quality and safety occurs, it can pose a problem for the survival of the company, by damaging consumer trust in the brand. On the other hand, providing high-quality and safe products and services that provide peace of mind can lead to stronger corporate competitiveness. Casio also believes that environmental conservation and contributing to a recycling-oriented society are corporate responsibilities.
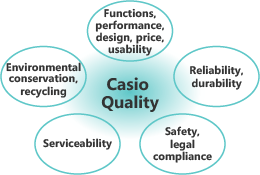
Policy
Quality Concept
Casio maintains a strong quality assurance system, based on its belief in "Quality First." This system requires all employees to make quality their first concern in every task they perform, enabling the company to offer products and services that please and impress customers. The company's commitment to quality supports its corporate growth and makes social contributions possible, while at the same time winning customers' trust and giving them peace of mind
Quality Management Policies
- To build a good corporate image, we offer products and services that please and impress our customers, gain their strong trust, and ensure their peace of mind.
- We respond to our customers' requests and inquiries with sincerity and speed, and reflect their valuable comments in our products and services.
- In all our business processes, we base our actions on the Principle of the Five "Gens"—in Japanese, genba (on site), genbutsu (actual goods), genjitsu (reality), genri (theory) and gensoku (rule)—and adhere to the basics of business operations.
- We capture and analyze quality assurance activities quantitatively, using reliable data, and use the analysis to make continuous improvements. We also maintain a quality information system that enables the sharing of quality information and prevention of problems before they occur, and prevents recurrence of quality problems.
System
In order to carefully maintain and improve Casio Quality, the company has created the quality assurance system shown in the diagram below. The Promotion Committee for Group-wide Quality Enhancement meets twice a year. It pursues activities such as making quality data accessible and easy to understand, and sharing quality information, while passing resolutions on quality policy and measures. The results are used for quality assurance activities.
Quality assurance system
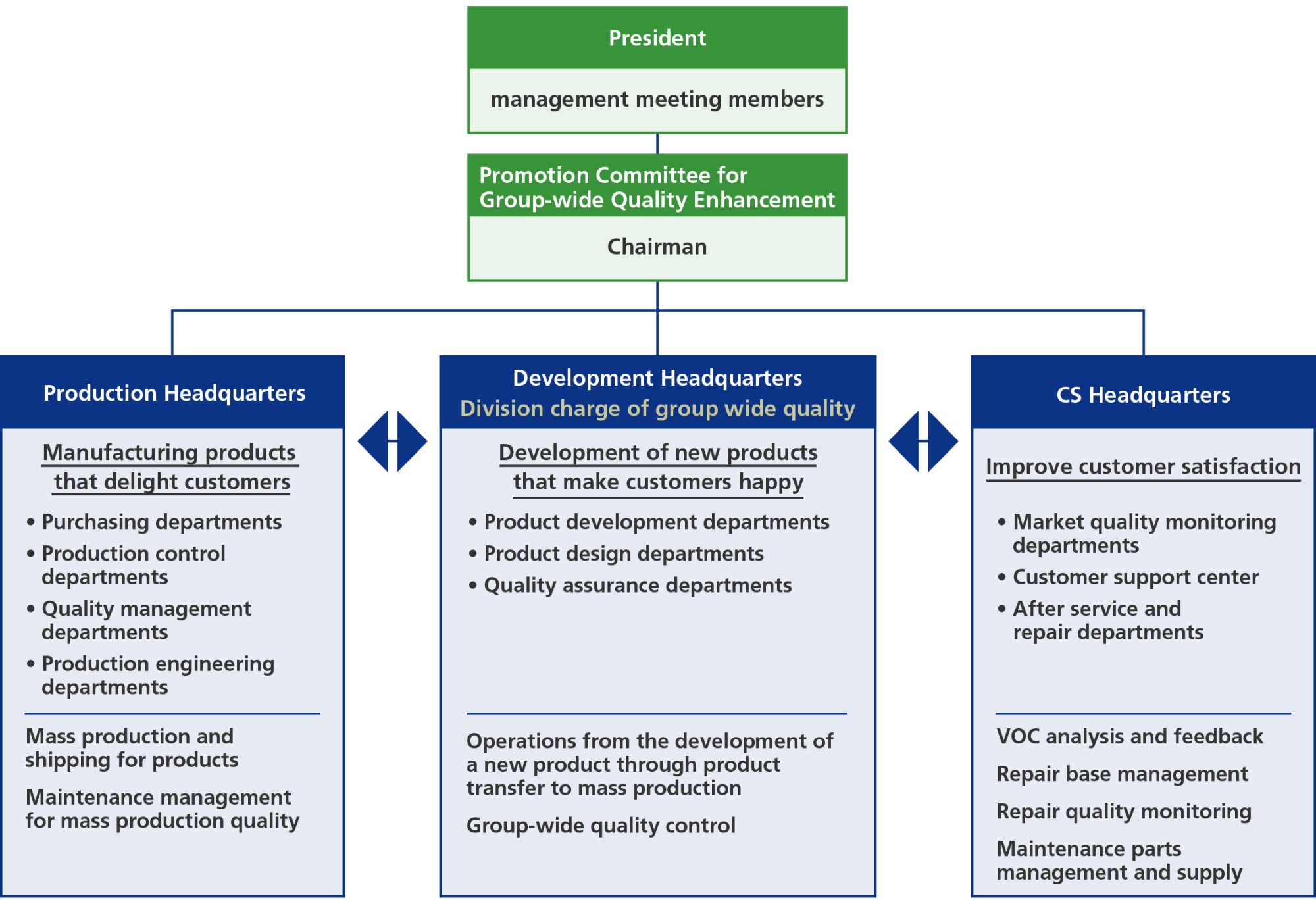
As the division in charge of group-wide quality management, the Development Headquarters is working hard to improve quality with the cooperation of the Production Headquarters and the CS Headquarters, while always pursuing the best solutions for customers.
The Casio Group shares the awareness that quality is the foundation of all operations, and the Promotion Committee for Group-Wide Quality Enhancement shares information on product quality, safety, and regulations in each country in order to raise the level of awareness across the entire group. An ISO 9001 quality management system is employed at all manufacturing sites using the PDCA cycle, and “quality-first proposals” are made, incorporating improvements to processes and quality. All of this is part of Casio’s tireless effort to maximize quality.
List of ISO 9001 Certified Sites
Classification | ISO 9001 Certified and Registered Sites |
Certified Date |
---|---|---|
Development, Production and Service Sites in Japan |
Yamagata Casio Co., Ltd. |
December 16, 1994 |
Casio Techno Co., Ltd. |
May 21, 2004 |
|
Production Sites outside Japan |
Casio Electronic Technology (Zhongshan) Co., Ltd. |
October 26, 2006 |
Casio (Thailand) Co., Ltd. |
July 13, 2012 |
|
Casio Electronics (Shaoguan) Co., Ltd. |
April 5, 2017 |
Activity Results
1. Front-loading activities
Casio has introduced and is using Design Review Based on Failure Mode (DRBFM) as a front-loading activity. This is a method for preventive activities. In this context, we are using 3D printers for pre-production verification based on digital analysis such as Computer Aided Engineering (CAE) analysis.* This has enabled us to achieve a reduction in the defect rate and the integration of design reviews and quality issues.
* CAE analysis is an analysis technique that simulates whether there are any performance issues with a product at the design stage.
2. Promotion of smart factories
As part of our efforts to promote smart factories, we are working to obtain more data on quality, processes and equipment. We perform analysis and forecasting based on the data we collect and store, and are achieving higher overall efficiency and reducing risks such as sudden stoppages.
3. Enhancement of in-house analysis operations
We have expanded our lineup of analysis equipment for use in analyzing defects in the market and for analysis during the design stage. (We have introduced an electron microscope, digital microscope, X-ray fluorescence analyzer, infrared spectrophotometer, transmission X-ray device, and thermal analysis device.) As a result, it has become possible to perform more accurate analysis (especially morphological observation and chemical analysis), and we are able to collect rapid and accurate data due to improvements in the image quality and sensitivity of the equipment. In addition, by implementing a combined analysis method (morphological observation, chemical analysis, physical property evaluation) as a method of analyzing phenomena, we can now estimate the mechanism of defect occurrence with high accuracy, which has led to faster responses to product improvements and problem solving, and to increased customer satisfaction.
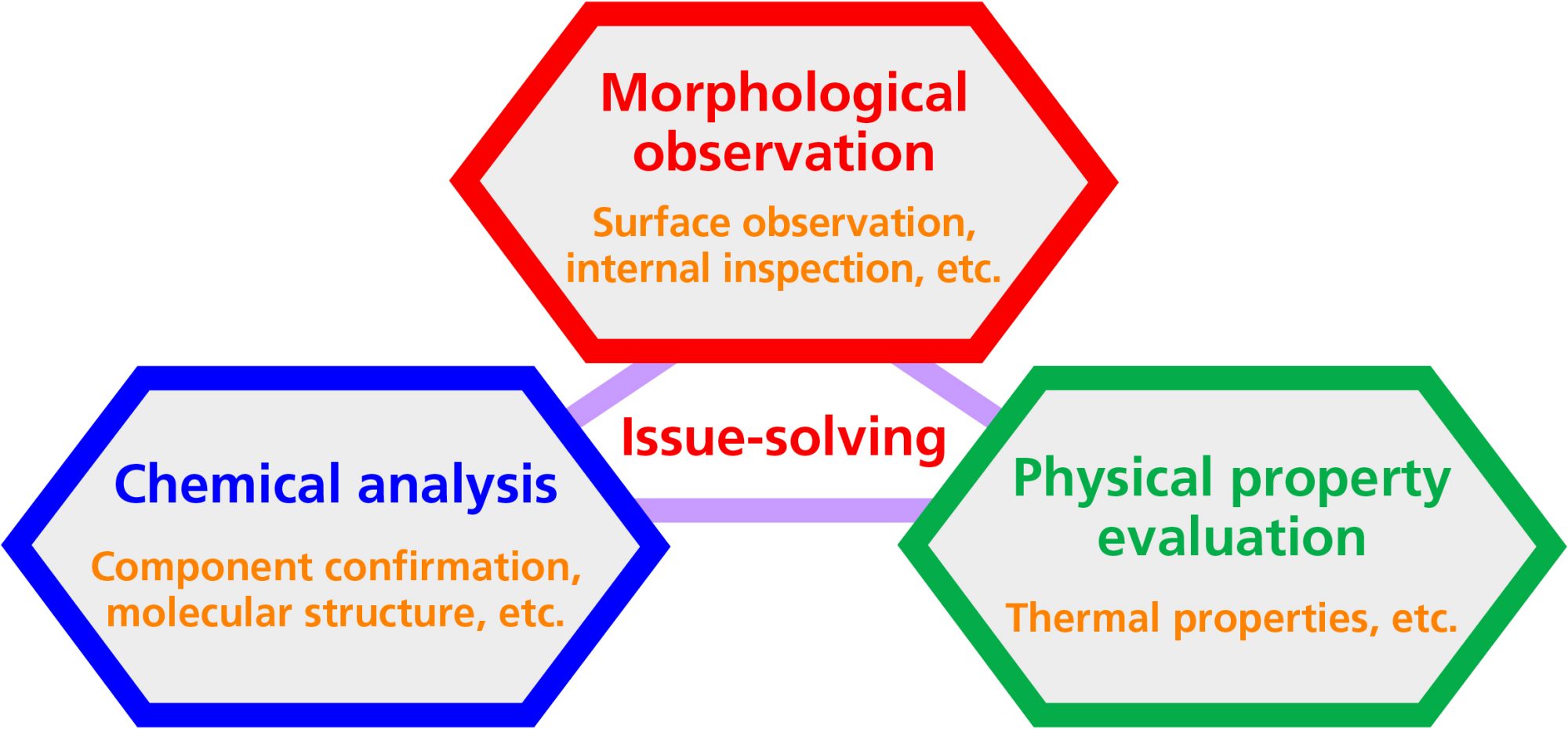
Offering Users Peace of Mind
Casio believes that safety is the most important aspect of its products, as it ensures the protection of customers’ property and person. As shown in the diagram below, Casio performs safety audits* at every stage, starting with product planning, and refers to the Product Safety Design Standards to ensure safety in the manufacturing process.
Accompanying the regular revision of the Product Safety Design Standards, we regularly revise the Product Safe Manufacturing Standards as well to guarantee safety.
* Safety audits: Design audits conducted based on the Product Safety Design Standards
Products that contain new technology components undergo a review based on the Safety Design Standards from the customer perspective.
Product safety system
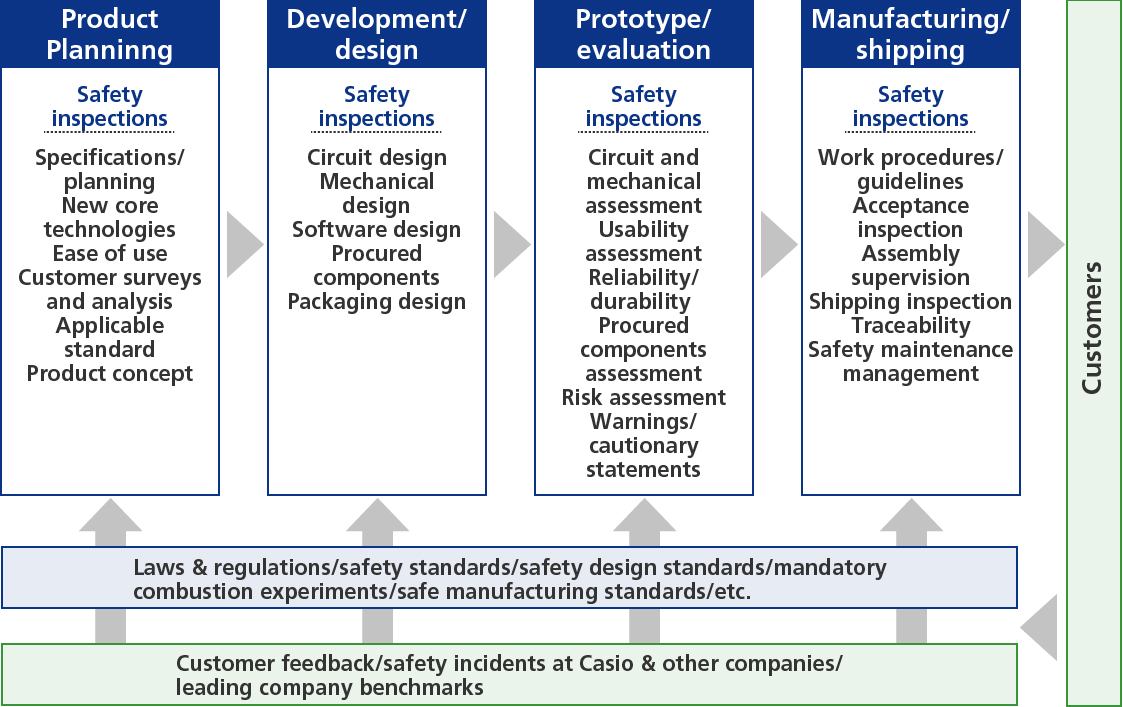
To comply with Japan’s Consumer Product Safety Act, which went into force on May 14, 2007, the Casio board of directors has adopted the Fundamental Policies on Product Safety. Based on these policies, Casio has put in place the Product Safety Voluntary Action Plan which specifies the details of the steps to be taken.
Casio takes all possible measures to prevent product quality problems and product-related accidents. However, in the unlikely event of a product-related accident or a quality problem, the company has clarified procedures for managing them and has established systems capable of responding appropriately as well as a response flow based on the in-house accident operating procedures. As shown in the diagram below, these include the prompt in-house communication of information, the issuance of notifications and reports to customers and relevant administrative agencies, and efforts to identify causes, corrective actions, and measures to prevent any future recurrence.
Response flow when a product accident or quality problem occurs
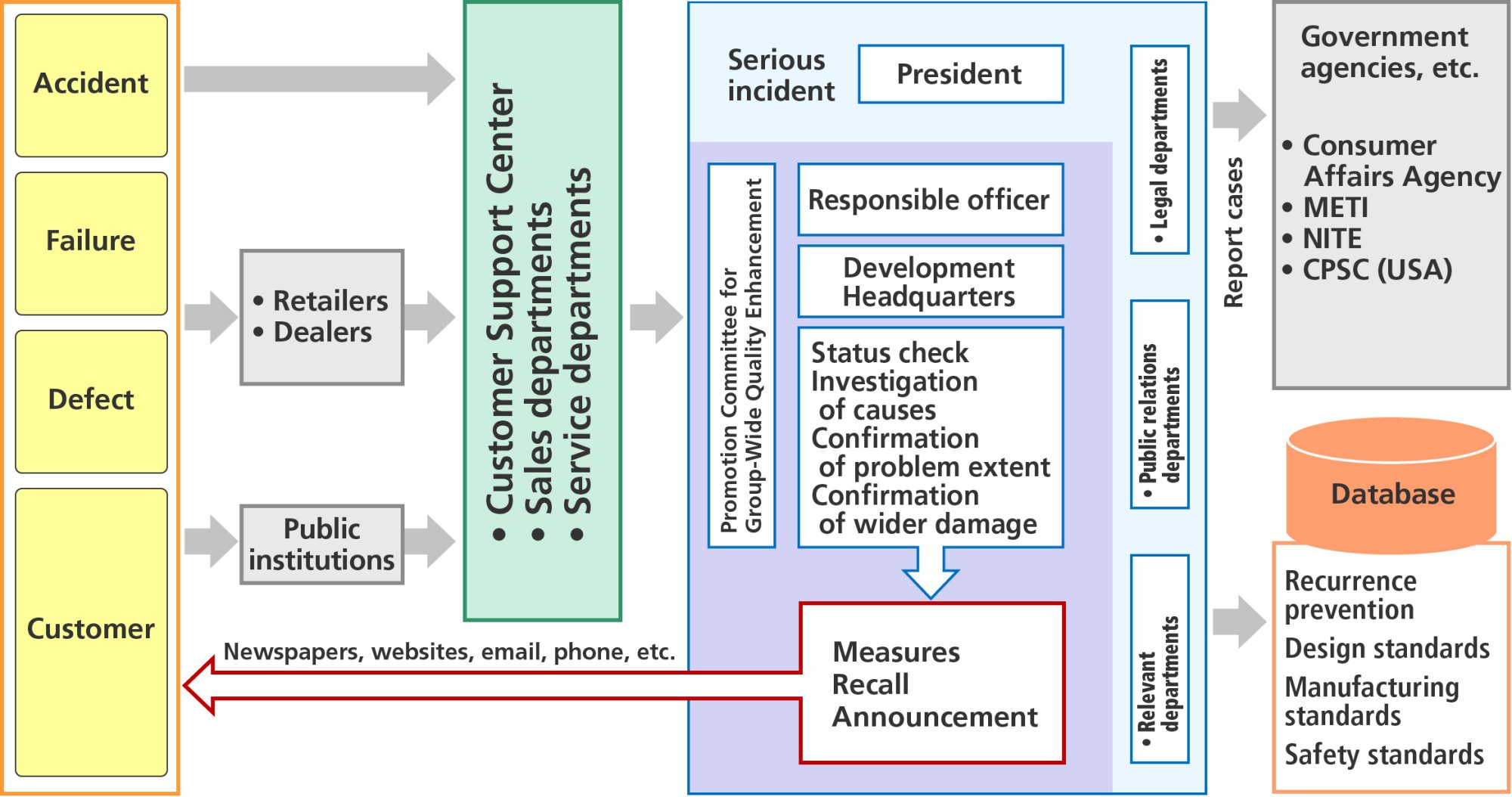
Education and Awareness Activities
It is very important that all employees have a strong awareness of quality so that Casio quality can be maintained. To this end, the first quality education program is given to all new employees. At the Group-wide Quality Enhancement Committee, Quality Managers’ Meeting, Market QC Meeting, and Manufacturing QC Meeting, the relevant departments share information and work on education and awareness raising activities from the standpoint of preventing recurrence of issues and taking preventive measures.
Providing Information on Safe Use of Products
Providing Product Information
Casio provides the appropriate information to customers to enable them to use the company’s product and services safely.
(1) Information is provided in the Precautions for Product Use section of user manuals.
(2) Information is provided in the Important Notifications on Product Safety section of the corporate website.
Providing Information on Laws and Regulations
Casio appropriately displays a mark that indicates the results of compliance with laws and regulations in the country where a product is sold. There were no violations of laws and regulations, voluntary regulations, etc., related to laws and regulations in each country in fiscal 2023 (April 2022 – March 2023).